Permatex 51813 vs 51817

If you are looking for a great sealant for your engine, consider Permatex 51813 or 51817. These products each contain an adhesive that is perfect for sealing your engine and have the capability to withstand high temperatures. They also come with a special lubricity agent that will help delay future problems with your vehicle’s engine.
When used on auto parts, they help protect the car while it runs. The Permatex sealants are versatile, SAFE to use, and a good value for the price. In this article, we will discuss Permatex 51813 vs 51817 to determine which sealant is better and how they compare to each other.
Permatex 51813 vs 51817: Main difference
Permatex 51813 is a clear silicone sealant, and Permatex 51817 is an anti-friction silicone sealant. These are both similar products in terms of forming a substance to protect from air and water. They do not differ in thickness or width.
Permatex 51813 | Permatex 51817 |
51813 used in rubber and plastic | Permatex 51817 is used to seal rubber components with a thickness of 0.2 inches or less in diameter |
Permatex 51813 is a faster-drying | Permatex 51817 is a slower-drying |
Permatex 51813 contains isopropyl alcohol | Permatex 51817 does not contain isopropyl alcohol |
Permatex 51813 also has the ability to withstand extreme heat and cold | Low heat stability |
Permatex 51813is can not resist abrasion, most chemicals, and oils. | Permatex 51817 is a silicone sealant that can resist abrasion, most chemicals, and oils. |
Anaerobic gasket maker Permatex 51813
When you need to seal an air leak, a leaky engine, or a hole in your wall with the Permatex 51813 valve gasket.
Permatex 51813 gasket maker is best for making airtight seals on hoses or other small- to medium-sized leaks. This type of gasket is also one of the most commonly used products in the automotive repair industry.
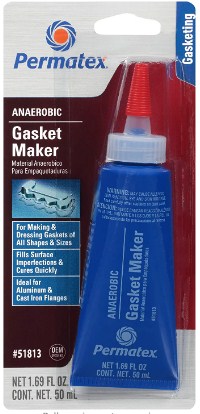
Features of the Permatex 51813 valve gasket include
- Aerodynamic design that minimizes friction and wears while sealing leaks.
- Comfortable grip handle for easy installation and removal. – Flexible rubber compound ensures wide application without too much stretching.
- Replacement valve gasket made of durable plastic material.
- Built-in sealing rings will seal most leaks.
Pros
- Gaskets are resistant to most chemicals in the automotive repair industry.
- The product requires little energy to create a seal.
- Gaskets are easy to cut with regular scissors or a Permatex gasket remover tool kit.
Cons
- Many users reported that valve gaskets must be sized properly to prevent leaks.
- This type of gasket is not resistant to oxygen or diesel fuels.
- Valve gaskets may become brittle due to UV exposure, which may result in cracking or tearing of the product.
What is Permatex 51813 used for?
Permatex 51813 is an extremely versatile and useful product. It is a silicone adhesive that can be applied to the inside or outside of your engine case, the radiator, clutch and transmission components, and more.
It provides superior adhesion for all uses with minimal shrinkage or distortion. It also has high elasticity due to its low viscosity which allows it to stretch out as it dries. The low viscosity also means that you can apply Permatex 51813 to large areas in a short period of time.
What is an anaerobic gasket maker?
An anaerobic gasket maker is a type of biogas. Biogas is any mixture of gases that are produced by the decomposition of organic matter, such as plants and animals. Gases in biogas decompose into products such as methane, carbon dioxide, water vapor, hydrogen sulfide, and other compounds.
Anaerobic gasket makers occur when microorganisms digest organic matter in areas without oxygen in order to create their own energy source.
Permatex anaerobic gasket maker cure time
Permatex Gasket Maker Cure time is a rubber type of sealant that cures within 1 hour. This chemical product cures in close to the same manner as a silicone elastomer sealant, but with more speed for gaskets and sealing surfaces.
Permatex anaerobic gasket maker temperature range
Permatex 3700 is a multi-purpose gasket maker, fuel additives, and engine coolant. Used by mechanics to seal engines, motors, and other mechanical systems, Permatex 3700 can also be used in radiators and oil pans to keep them from freezing.
Permatex 3700 is a combination of Permatex 3700 and Permatex 5100. This formula allows for greater working fluid choice and resistance to freezing. It is considered the most versatile gasket maker available.
The ability to seal engine cooling systems with cold engine oil, vacuum or compressed air without freeze-up can be obtained by using high-quality Permatex 3700 high-temperature sealant technology.
What are anaerobic sealers?
Anaerobic sealers are used to coat and bond large areas, such as concrete floors and ramps. They work by creating a polymer coating that acts like glue to bind the two surfaces together. This allows them to make up for the pores in the surface of the concrete that would otherwise be lost during pouring.
Using this method, it is possible to apply a sealer on an area larger than 100 square meters, which would be impossible using traditional methods.
It is also possible to apply this type of sealer using much lower levels of water, resulting in a thinner coating. This makes the sealer process more environmentally friendly and less expensive to operate.
Ergonomics is another benefit, as the surface becomes harder and more durable through the application of anaerobic sealers.
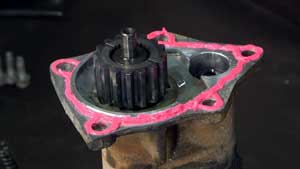
How does anaerobic sealant cure?
Anaerobic sealant is the ultimate graffiti-proof and weatherproof protection, making it better than paint. It is a polymer developed from natural gas and it is installed by employing high-pressure cleaning devices to remove any loose material on your walls.
The sealant is then applied directly onto the surface of the wall, and once it is dry, it will only be visible if it was done in a previous paint job.
What is the difference between an anaerobic sealant and RTV?
Anaerobic sealant is a rubber product used to prevent water intrusion and slow the curing. When RTV is applied, it will cure without the need for an outside source.
RTV adheres to surfaces better than anaerobic sealants because one needs a hot and humid environment to cure both types of sealants.
1. Anaerobic sealant:
A rubber product that stops water from getting in your door or window frame by forming a barrier that would otherwise allow moisture or air penetration. It is semi-permanent, meaning it can be removed without damaging surfaces or requiring much effort.
An anaerobic sealant product should withstand temperatures ranging from -40 degrees to 180 degrees Fahrenheit (-40 degrees Celsius to 82 degrees Celsius).
2. RTV:
A compound that cures under pressure, RTV is a room-temperature vulcanizing silicone, which means that it has a shelf life. The time frame for shelf life is approximately two years from the date of manufacture. RTV is a rubber product that takes 24 hours to cure under ideal conditions.
RTV does not require an outside source, such as heat or sunlight, for curing. If a part or object is covered by RTV and then sealed in a container, the object will no longer require an outside cure source once it has been opened after the allotted amount of time has passed.
How long does it take anaerobic sealant to cure?
The curing time depends on the thickness of the material it is used on and its temperature. The degree of curing is also affected by quality and type, as well as ambient temperature.
Typically, a sealant cures for about one hour at 250 F to 400 F or less depending upon its thickness. If the application is thicker or colder than this range it will take longer to cure. As mentioned above, the actual curing time also depends on the temperature of your installation.
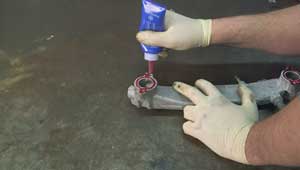
Read More Are Foam Sealants Safe For Siding
What is non-corrosive gasketing?
Gasketing is an industrial process that seals metal surfaces and protects against corrosion. This may be done by applying a coat of molten metal on a surface, or by covering it with a highly corrosion-resistant coating.
A non-corrosive gasketing material is meant to seal or cover metal surfaces that are exposed to corrosive elements in an inside environment such as chemical processing, water treatment facilities, wastewater treatment plants, and industry, and manufacturing plants.
Non-corrosive gasketing is different from other types of gaskets that are also used for sealing, including:
Many different materials can be used to create non-corrosive gaskets depending on what is needed to function as a seal inside. To be effective in an industrial environment, non-corrosive gaskets need to be formulated with corrosion-resistant and static dissipative elements.
What is an OEM gasket?
An OEM gasket is one that was designed with the same specifications as a product we manufacture, or can replace an original equipment manufacturer’s part. Gaskets are usually made of rubber, silicone, or other elastomeric material and are used to seal surfaces in all kinds of machines.
A small number of gaskets are also made with a metallic material to provide additional strength and durability. Nearly all gaskets manufactured in the U.S. are made by one of five companies: A T I, AGT, Arrex-Lon, Advance, and Vollrath.
Because the majority of these gasket manufacturers are located in the U.S., most gaskets that have been manufactured overseas have had an aftermarket rubber or silicone replacement installed when they returned to their original owners.
Permatex anaerobic gasket maker 51817
51817 is a very good product. It has different functions and can be used for many different purposes. Permatex anaerobic gasket maker 51817 is mainly used for clapping joints together in cars, trucks, motorcycles, watercraft, and other vehicles.
Permatex anaerobic gasket maker 51817 is a great product. If you have used this product long enough, you should be able to stop using it and get something new, since it is not supposed to be refurbished. Permatex anaerobic gasket maker 51817 is made from pre-measured anaerobic sealant that lets you apply Permatex even where heavy grease and previous seals can’t.
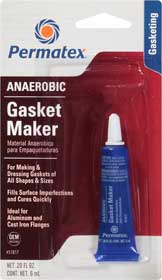
Read More About: Will Froth Pak Foam Sealant Catch On Fire
Features
- This product is clear and doesn’t have any chemical smells.
- The sealant is non-hardening and it is water-resistant, which makes it last longer.
- The sealant has a rubber-like consistency when you apply it.
- Permatex anaerobic gasket maker 51817 can be used to form a permanent, waterproof seal on almost any surface. It will not shrink or crack and provides protection against vibration and shock.
- Permatex anaerobic gasket maker 51817 is easy to use and quick to dry.
Pros
- The sealant is non-hardening and it is water-resistant, which makes it last longer.
- The sealant has a rubber-like consistency when you apply it.
- Permatex anaerobic gasket maker 51817 can be used to form a permanent, waterproof seal on almost any surface.
- The sealant will not shrink or crack and provides protection against vibration and shock.
Cons
- The sealant may come off if you put it on too thinly and it may not cure properly.
- The sealant can get into your eyes and make them water.
Permatex 51817 specifications
This thread-locking compound is a heavy-duty formula for use in applications such as performance racing, heavy-duty trucking, and construction
The odorless formula minimizes the risk of smelling like petroleum products. Excellent rust and corrosion protection with long-term sealant capabilities when applied to metal surfaces.
It’s designed for maximum strength to withstand engine vibration, road shock, and extreme weather conditions. It is formulated for exceptional rust, corrosion, and swelling protection, with added friction to prevent wear and tear on the bolt threads.
It is recommended for applications where bond strength must be maintained under extreme conditions of heat, cold, or vibration.
Permatex Pro Tips – Selecting the Right Gasket for an Exhaust Manifold Replacement
Final Word
Permatex 51813 vs 51817, The main difference between these two products is the solvent. The epoxy resin is composed of polymer chains that have a water-soluble group.
It’s common to use a water-based solvent in order to remove the water-soluble group from the polymer chains, and this allows for easier processing and disposal of used epoxy resins. We hope you find this article useful, and good luck! Leave a comment on what you think of this article.